3 Gallon Liquid Glass Epoxy Clear Pour Resin Clear Epoxy for Floors
-
$5.61 / 5 - 999 sets
$5.37 / 1000 - 9999 sets
$5.13 / >=10000 sets - 5 sets
- Huizhou Jincheng Composite Materials Co., Ltd.
- Guangdong, China
- Ms Shannon F
Product Detail
EINECS number: | 231-072-3 | type: | two components |
port: | Shenzhen | main ingreadient: | epoxy resin |
place of origin; place of origin: | Guangdong, China | Supply capacity: | 10 tons per day |
IF: | C15H16O2C2H7ONC3H5OCl | model: | 1201AB |
Material: | epoxy resin | Other names: | epoxy resin |
The mixing ratio: | A:B=1:1 | application: | decorate |
MOQ: | 1 gallon | usage: | Construction, Fibers & Clothing, Footwear & Leather, Packaging, Shipping, Carpentry, Decoration |
color: | transparent | CAS number: | 38891-59-7 |
Package preview: | Shelf life: | 6 months | |
Packaging Details: | 5kgs/bottle and 20kgs/set 20kgs, 25kgs and 200kgs are also available. | feature: | DIY |
payment terms: | L/C, Western Union, D/P, T/T, Paypal | Classification: | two-component adhesive |
brand: | jessie |

We manufacture advanced epoxy resins that contain UV protection stabilizers to prevent yellowing. As artists ourselves, we want to know we're working with a fresh, high-quality product. Unlike competing products, all JinCheng resins are labeled with a brew date so you can tell how old your product is. We stand behind all our products 100%
describe
part( 1201) | One | Second | |
color | transparent | transparent | |
Viscosity (25°C) | 2000-4000CPS | 100 Max CPS | |
The mixing ratio | A: B = 1:1 (weight ratio) | ||
hardening condition | 25℃×8H to 10H or 55℃×1.5H (2g) | ||
available time | 25℃×40min (100g) | ||
Hardness, Shore D | <86 | ||
Bending strength, Kg/mm2 | 28 |
detailed image
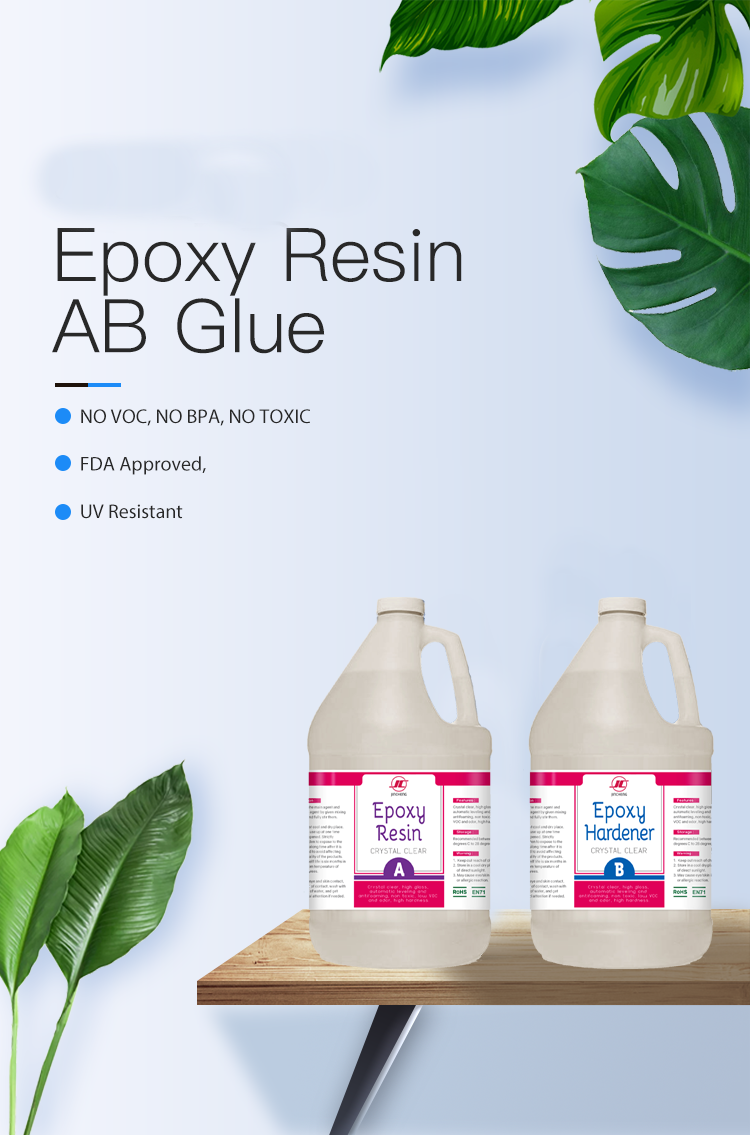
Our factory supports customized OEM/ODM product packaging of various specifications
If you would like a free sample, please click here.
If you would like a free sample, please click here.
If you would like a free sample, please click here.
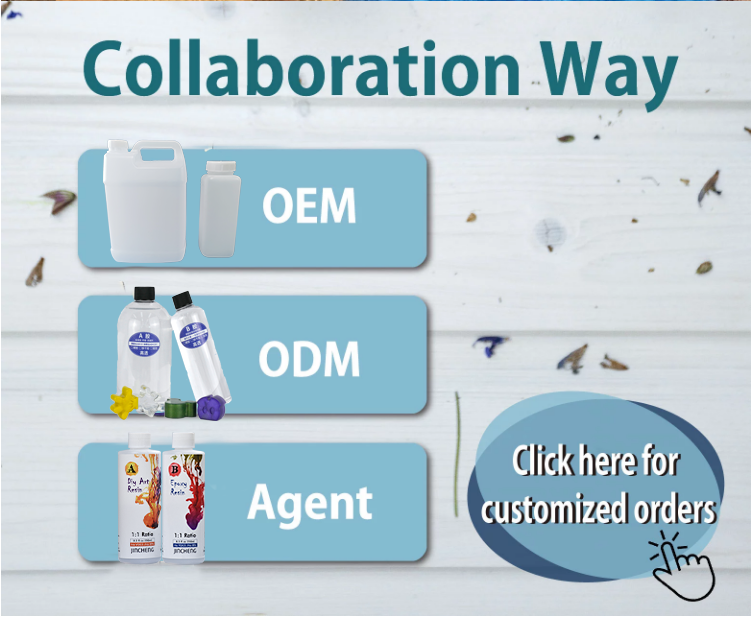
Easy-to-use 1:1 formulation, no experience required
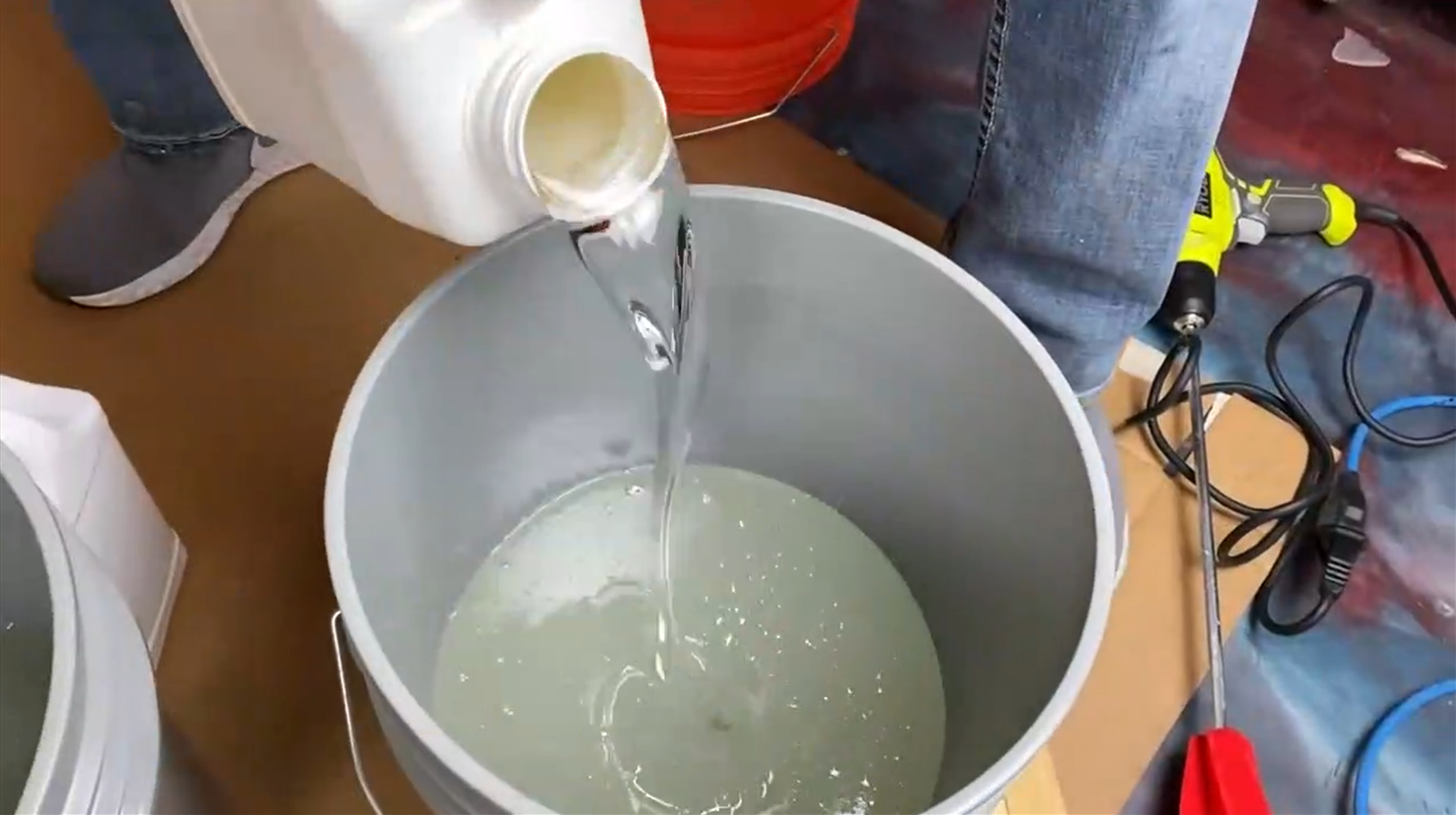
Step 1: Measure
Pour equal parts resin and hardener into a clean mixing container or graduated mixing bucket, using a 1:1 ratio by volume
It is crucial to measure the product accurately and mix it thoroughly. Measure 1 part resin and 1 part hardener by volume. don't want
Change this ratio. Our epoxies are formulated to cure in specific mixing ratios, any variance may result in a product that will never
Completely healed. We recommend always pouring the hardener into the mixing container before pouring the resin. This will help
The two ingredients are thoroughly mixed.
Pour equal parts resin and hardener into a clean mixing container or graduated mixing bucket, using a 1:1 ratio by volume
It is crucial to measure the product accurately and mix it thoroughly. Measure 1 part resin and 1 part hardener by volume. don't want
Change this ratio. Our epoxies are formulated to cure in specific mixing ratios, any variance may result in a product that will never
Completely healed. We recommend always pouring the hardener into the mixing container before pouring the resin. This will help
The two ingredients are thoroughly mixed.

Step 2: Mix
First Mix: Mix with a flat-bottomed stick or spatula, being sure to scrape the sides and bottom of the container as you mix. Your
The mixture will appear cloudy at first, then become more transparent as the resin and hardener molecules begin to mix in it
Three to five minutes.
Second mix: Pour the resin and hardener from the first container into the second container, scraping all the mixture out of the container
sides and bottom of the cup. Mix thoroughly for another three minutes.
First Mix: Mix with a flat-bottomed stick or spatula, being sure to scrape the sides and bottom of the container as you mix. Your
The mixture will appear cloudy at first, then become more transparent as the resin and hardener molecules begin to mix in it
Three to five minutes.
Second mix: Pour the resin and hardener from the first container into the second container, scraping all the mixture out of the container
sides and bottom of the cup. Mix thoroughly for another three minutes.

Step 3: Seal Coat Phase
The best way to apply the seal coat is to start at one end of the bench and pour the resin along the entire length of the surface in a zigzag pattern
when you go. Then use a foam brush to drag the resin across the entire surface for an even coating. epoxy resin curing
Quickly puts in containers so it is necessary to apply the seal coat quickly or mix a small amount so that it does not cure
in the container while you're still using it. The sealer does not need to be smooth as the waterproof layer will fill
Brush strokes and irregularities make it clear. After the entire surface is sealed, wait 4-6 hours to pour the flood paint
Ton. Do not exceed 10 hours, or the waterproof coating may not blend perfectly into the seal coat.
The best way to apply the seal coat is to start at one end of the bench and pour the resin along the entire length of the surface in a zigzag pattern
when you go. Then use a foam brush to drag the resin across the entire surface for an even coating. epoxy resin curing
Quickly puts in containers so it is necessary to apply the seal coat quickly or mix a small amount so that it does not cure
in the container while you're still using it. The sealer does not need to be smooth as the waterproof layer will fill
Brush strokes and irregularities make it clear. After the entire surface is sealed, wait 4-6 hours to pour the flood paint
Ton. Do not exceed 10 hours, or the waterproof coating may not blend perfectly into the seal coat.

Step 4: Waterproof jacket stage
The self-leveling thickness of each coat of waterproofing is approximately 1/8 inch. If thicker than 1/8 inch is required, multiple coats will be required. you
You must wait at least 4 to 10 hours between waterproofing coats. The epoxy will still be tacky so the next pour will stick to it.
The best way to apply a waterproof coat is to start at one end and pour the resin over the entire length of the surface, zigzag in your direction
go. After pouring, put the container down. Don't try to scrape anything else out of the barrel. Because you are
Pour about three times the amount of seal coat product and the material will begin to flow out immediately.
The self-leveling thickness of each coat of waterproofing is approximately 1/8 inch. If thicker than 1/8 inch is required, multiple coats will be required. you
You must wait at least 4 to 10 hours between waterproofing coats. The epoxy will still be tacky so the next pour will stick to it.
The best way to apply a waterproof coat is to start at one end and pour the resin over the entire length of the surface, zigzag in your direction
go. After pouring, put the container down. Don't try to scrape anything else out of the barrel. Because you are
Pour about three times the amount of seal coat product and the material will begin to flow out immediately.

Step 5: Remove Air Bubbles
Once you've adequately covered the entire surface with your waterproof coat, you'll begin the process of popping the air bubbles. This
The best tool for removing air bubbles is a small propane torch. Hold the flame about 6 to 10 inches from the table, and
Use quick ironing motions to sweep across entire surface. You will immediately see the bubbles start to pop. do this until
All air bubbles disappear from the surface of your table.
* Bubbles usually form after pouring epoxy. Foam can continue to develop after 60 minutes
The curing process has started. The most effective way to remove them is to occasionally spray 10 - 15 sprays on the surface with a blowtorch
Minutes at a time.
Once you've adequately covered the entire surface with your waterproof coat, you'll begin the process of popping the air bubbles. This
The best tool for removing air bubbles is a small propane torch. Hold the flame about 6 to 10 inches from the table, and
Use quick ironing motions to sweep across entire surface. You will immediately see the bubbles start to pop. do this until
All air bubbles disappear from the surface of your table.
* Bubbles usually form after pouring epoxy. Foam can continue to develop after 60 minutes
The curing process has started. The most effective way to remove them is to occasionally spray 10 - 15 sprays on the surface with a blowtorch
Minutes at a time.

Step 6: Curing Process
After the final coat has been applied, the product should be stored in a clean, dust-free environment at a temperature of at least 75-80°F. This
Product takes approximately 12-14 hours to dry to the touch. However, this product should not be put into use in any
Three days for it to harden enough to resist scratches. At temperatures below 75 F, the product will
Takes longer to cure and may not fully cure.
After the final coat has been applied, the product should be stored in a clean, dust-free environment at a temperature of at least 75-80°F. This
Product takes approximately 12-14 hours to dry to the touch. However, this product should not be put into use in any
Three days for it to harden enough to resist scratches. At temperatures below 75 F, the product will
Takes longer to cure and may not fully cure.
*Not suitable for outdoor use
NOTE: All epoxies have natural color variations or shades. The color of epoxy-coated surfaces may fade or accentuate
tone. White surfaces are always the most challenging in terms of accentuating the tone of the epoxy. white itself has a lot
tone. The appearance of white surfaces coated with epoxy is also most affected by lighting. LED example
"Daylight" bulb lighting compared to "soft/warm" lighting.
NOTE: All epoxies have natural color variations or shades. The color of epoxy-coated surfaces may fade or accentuate
tone. White surfaces are always the most challenging in terms of accentuating the tone of the epoxy. white itself has a lot
tone. The appearance of white surfaces coated with epoxy is also most affected by lighting. LED example
"Daylight" bulb lighting compared to "soft/warm" lighting.
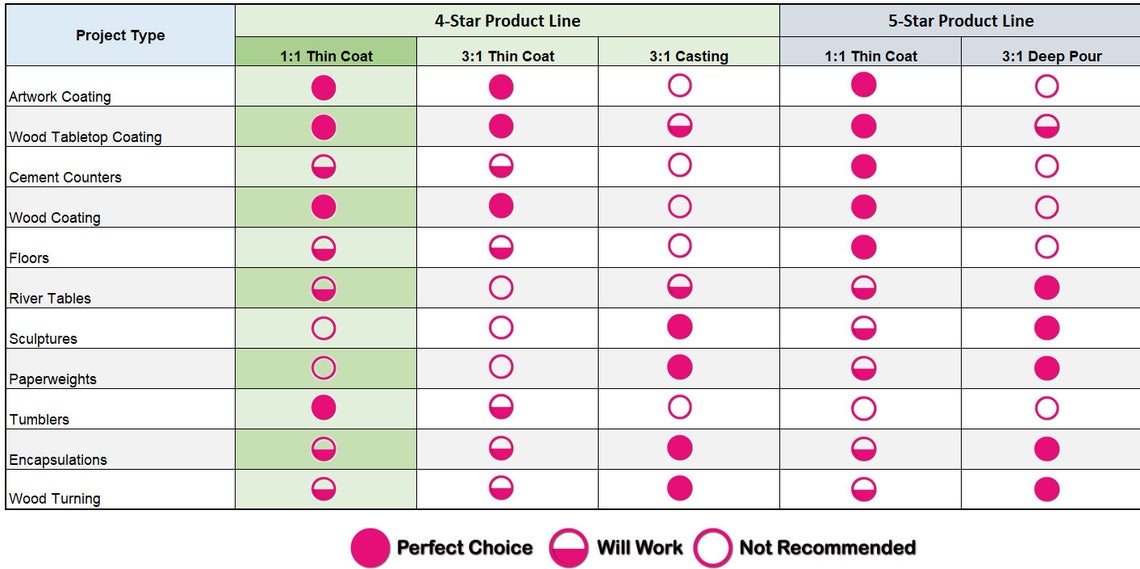

Epoxy resin for floors

Title here.
Semi-automatic PET Blow Molding Machine Blow Molding Machine PET Bottle Making Machine is suitable for producing PET plastic containers and bottles in various shapes.

Simple and fast application:
Color epoxy is a two-component system. 2:1 ratio.
Each specially packaged kit contains 3 cans, 2 resin parts "A" and 1 hardener part "B".
Each order comes with step-by-step mixing and application instructions.
The pot life of the colored epoxy is 40 minutes.
Each specially packaged kit contains 3 cans, 2 resin parts "A" and 1 hardener part "B".
Each order comes with step-by-step mixing and application instructions.
The pot life of the colored epoxy is 40 minutes.
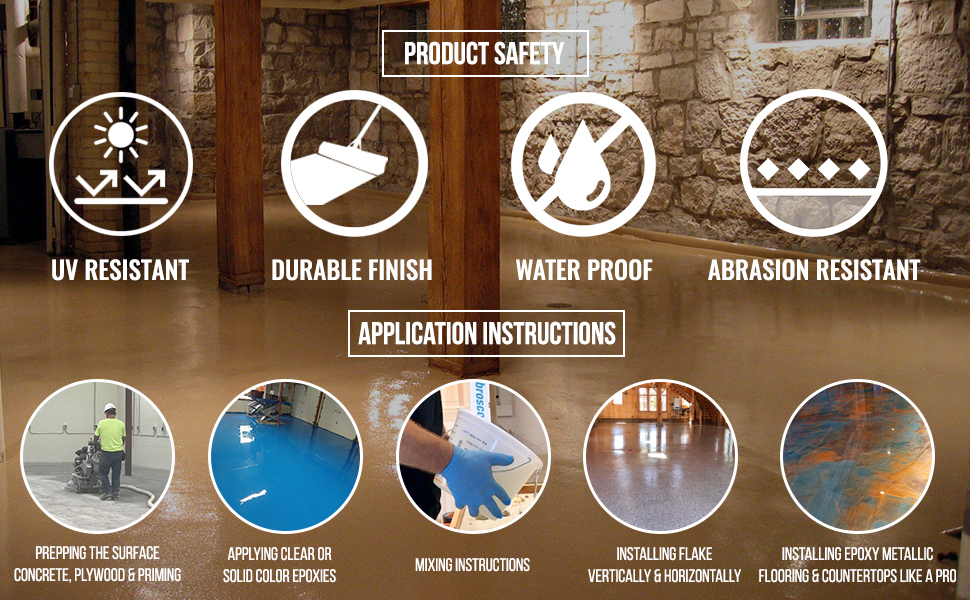
Colored Epoxies is a manufacturer of custom modified two-component flexible epoxy flooring systems with a 2:1 mix ratio. 2 parts A resin to 1 part B hardener. Color epoxy resins are 100% solids and VOC free. Colored Epoxies uniquely formulates its cycloaliphatic resins and modified cycloaliphatic curing agents with the strongest UV protection and chemical resistance on the market. Coloredepoxies is the trusted number one choice of epoxy professionals when installing epoxy metal floors, sheet floors, solid colored floors, countertops and more. Dip and roller coverage is 350 sq. ft. per gallon, with squeegee applications ranging from 125-175 sq. ft. per gallon. Use tinted clear or tinted epoxy resins as PRIMER/MVB moisture barrier coatings and topcoats. No additional primer required! ColoredEpoxies Installation Instructions are included with every purchase and you will learn step by step all of the unique application techniques from prepping concrete surfaces to primer, multicolor metal installation, flake coverage, various flake sizes, mica, quartz and glitter Easy to follow pictographic layout.
VIEW MORE
Related Products
-
Liquid Epoxy Resin Raw Material Price Industrial Resin Epoxy Resin Curing Agent Chemicals
Viscosity: Resin 1600cps Curing agent 100cps IF: C15H16O2C2H7ONC3H5OCl Package preview: Origin: Guangdong, China EINECS number: 230-391-5 Classification: Two-component adhesive Minimum order quantity: 20kg color: transparent model: YD-128 Chemical Abstracts Service number: 7085-85-0 usage:...... -
High Penetration Clear Epoxy Resin for Outdoor Gravel Driveway Epoxy Aggregate Paving Stone Floor Coating Resin 20kg Kit
Shelf life: 6 months Classification: Two-component adhesive Original Equipment Manufacturers: Provide OEM/ODM/label customization services Packaging Details: 15KG/3 gallon kit; 1.5 gallon; 5kg, 20kg kit; 25kg; 15 gallon; 200kg. Support OEM/ODM customization. Origin: Guangdong, China usage: Suitable.... -
Recina Epoxica Para Pisos Epoxy AB Glue Self-Leveling Floor Kit for Concrete and Cement Floor Coating
Product Category: 2 parts Chemical Abstracts Service number: 38891-59-7 Place of origin: Guangdong, China port: Shenzhen feature: Good fluidity, low viscosity, bright surface Performance: No yellowing Supply capacity: 1000 tons per month color: transparent Classification: Two-component adhesive...... -
Crystal AB glue epoxy resin/transparent liquid epoxy resin
The mixing ratio: A:B=3:1 model: 318AB-9 Feature 1: Automatic defoaming Origin: Guangdong, China type: epoxy resin Packaging Details: 5kg per bottle; 20kg/carton 20kg/barrel 200kg/barrel Delivery time: 3 days color: to clear usage: Construction, Fibers and Clothing, Footwear and Leather, Packaging,.... -
Crystal Clear/Epoxy-Resin-Table-Top Deep Casting Epoxy Resin Suppliers
payment terms: L/C, Western Union, D/P, T/T, Paypal The mixing ratio: A:B=3:1 EINECS number: 231-072-3 Other names: epoxy resin CAS number: 38891-59-7 Material: epoxy resin Package preview: IF: C15H16O2C2H7ONC3H5OCl Classification: two-component adhesive type: two components model: 312AB-6-N usage:.... -
Transparent 3d epoxy floor paint transparent epoxy resin liquid resin
The mixing ratio: A:B=3:1 payment terms: Western Union, T/T, MoneyGram main ingreadient: epoxy resin usage: Construction, Fibers and Clothing, Woodworking brand: De Jianbang Supply capacity: 100,000 kg per month IF: mixture color: Transparent liquid port: Qingdao/Shanghai/Yiwu/Shenzhen CAS number:..... -
Holographic Glitter Floor Coating Epoxy Glitter Floor
EINECS number: other Classification: two-component adhesive brand: Mountain bike JZJ product name: Holographic Glitter Floor Coating Epoxy Glitter Floor CAS number: 61788-97-4 payment terms: L/C, Western Union, D/P, D/A, T/T, MoneyGram color: to clear usage: Construction, transportation, floor...... -
Rhinestone crafts multi-purpose strong glue cloth metal stone manicure wood glass B7000 jewelry bead glue
Package preview: MOQ: 3 payment terms: Western Union, T/T Origin: China sample: available delivery time: within 5 working days OEM/Design Manufacturer: OEM ODM private label model: M42 main ingreadient: acrylic fiber product name: B7000 glue Pay: Trade Assurance. Western Union. TT Packaging...... -
Strong glue ab glue transparent liquid crystal epoxy resin good quality and good price
port: Hong Kong port usage: put up color: Colorless translucent/colorless transparent Density (g/m3): 1.07+0.05/0.95+0.03 type: Resin 312A-H3/curing agent 312B-H3, AB glue Other names: Adhesive IF: [CH(CH2Cl)CH2O]n Classification: other adhesives model: 312AB-H3 brand: benu Mixing ratio (weight...... -
Spray Foam Insulation Polyurethane Foam Kit (650-215 Board Feet) Izotup 200 Quick Rise (QR) with Mask Cylindrical Tube Material
payment terms: wire transfer usage: Construction, Fibers and Clothing, Footwear and Leather, Packaging, Transport, Carpentry Name: Spray Polyurethane Foam Kit Foam Type: Obturator type: closed cell foam size: 41 lbs / 16" x 16" x 9" / 215 BdFt Classification: two-component adhesive EINECS number:......